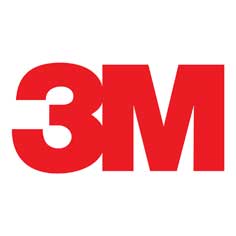
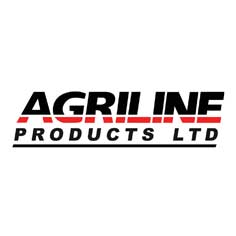
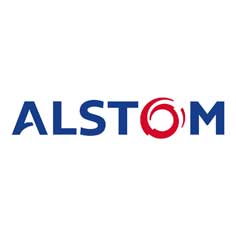
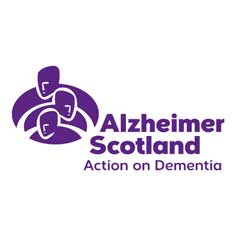
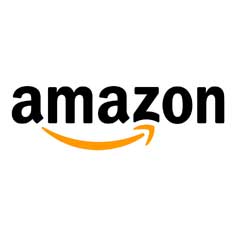
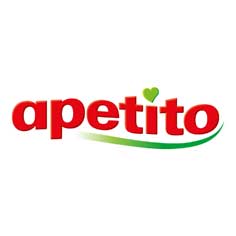
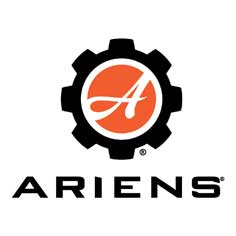
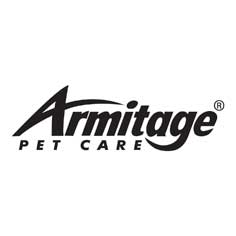
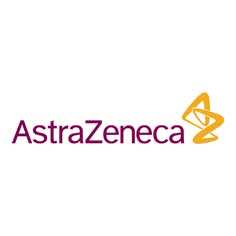
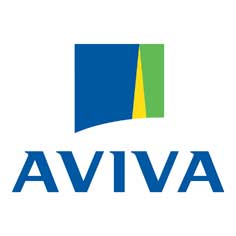
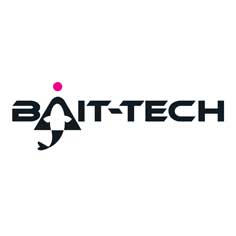
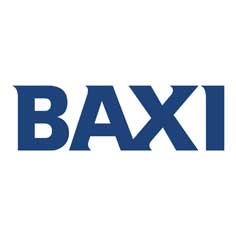

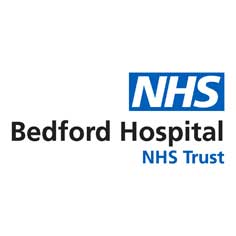
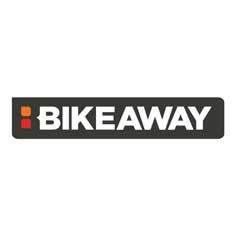
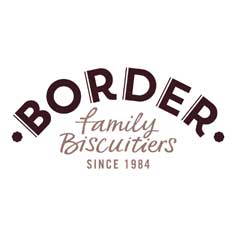
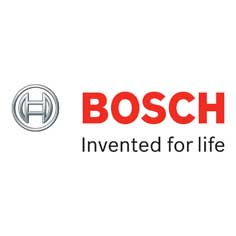
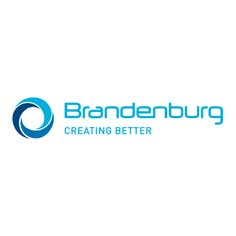
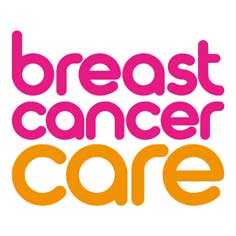
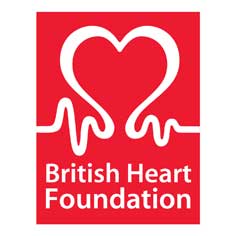
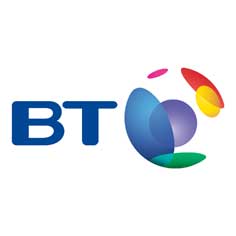
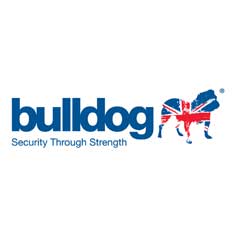
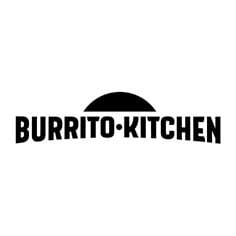
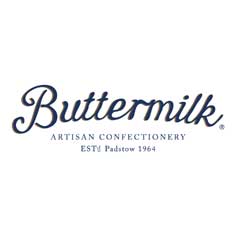
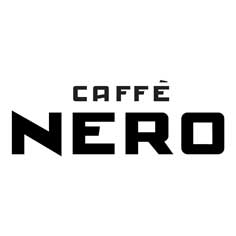
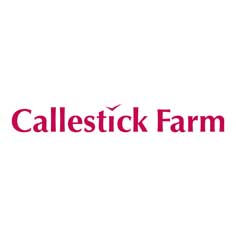
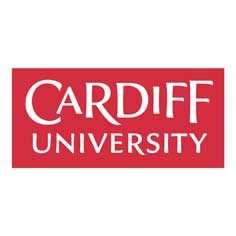
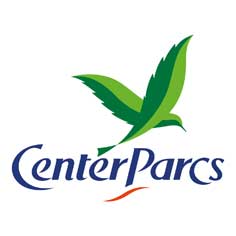
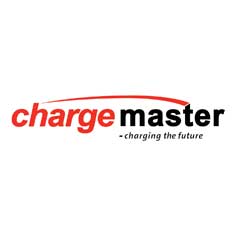
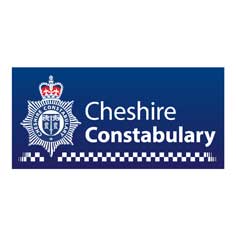
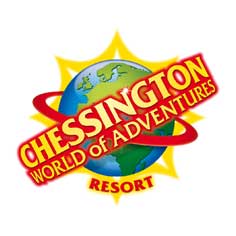
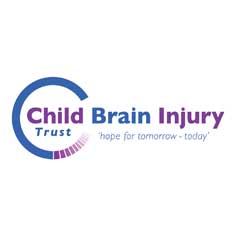
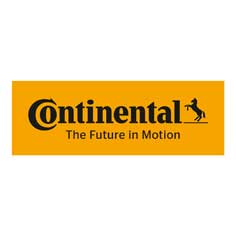
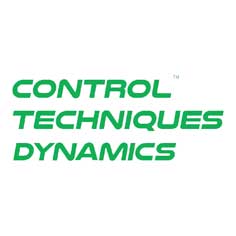
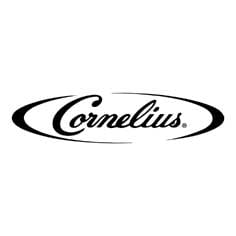

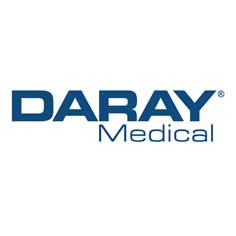
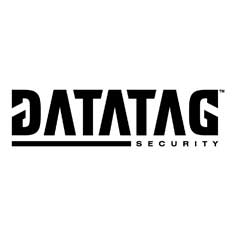
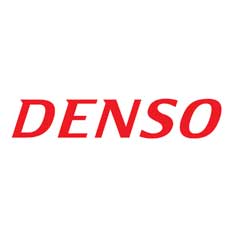
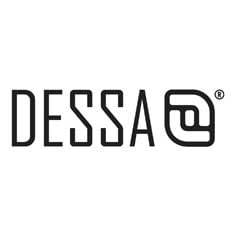
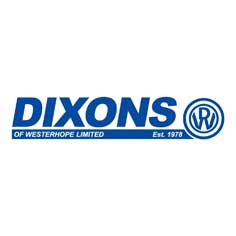
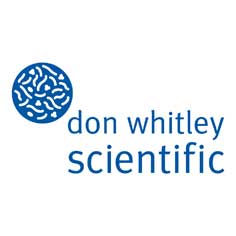
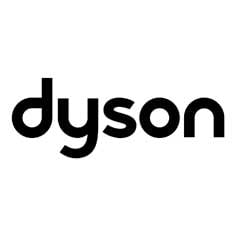
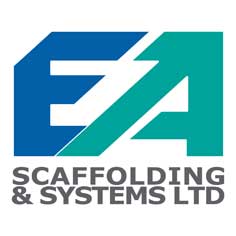
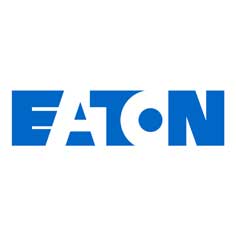
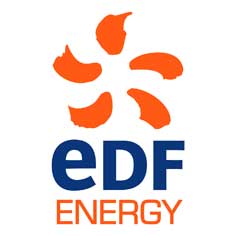
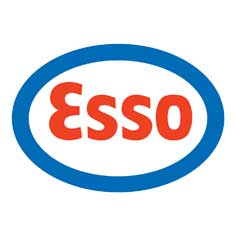
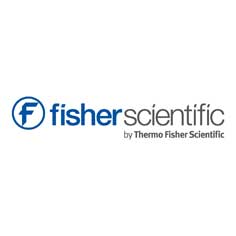
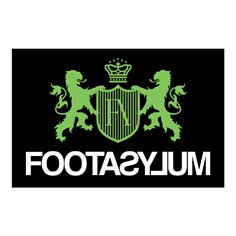
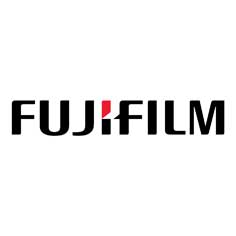
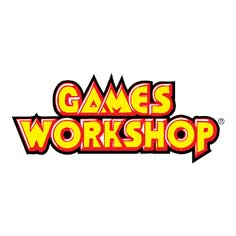
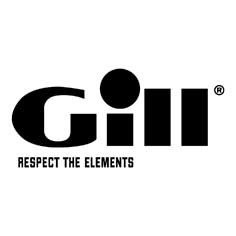
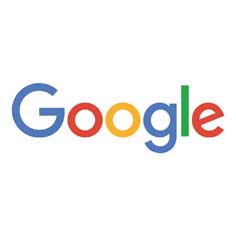
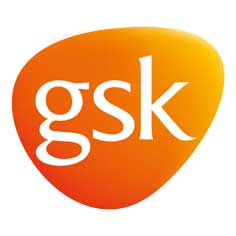
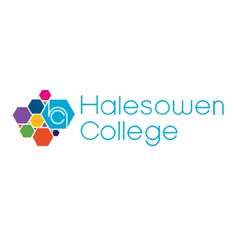
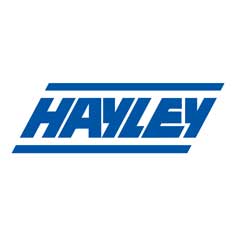
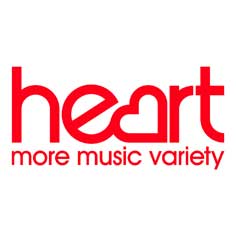
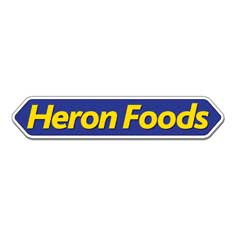
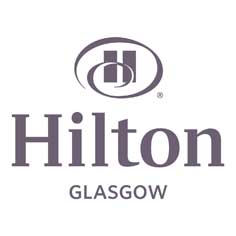
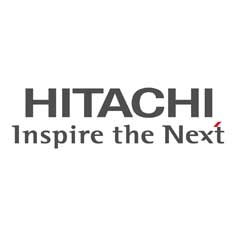
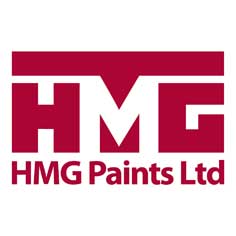
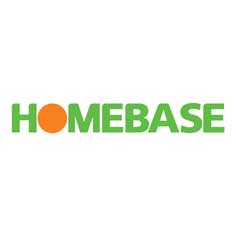
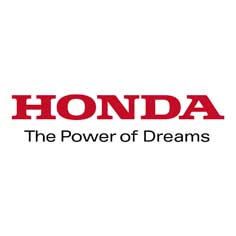
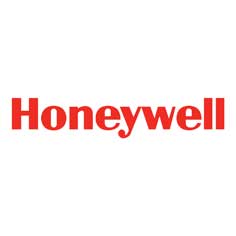
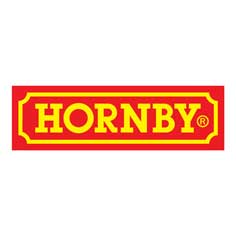

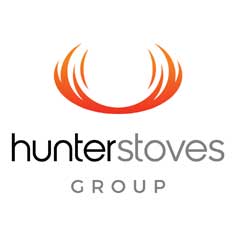
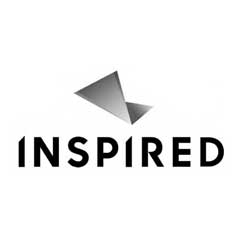
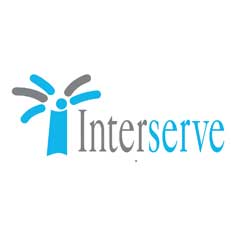
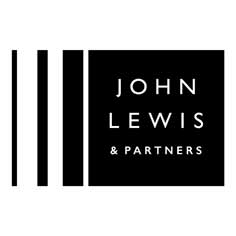
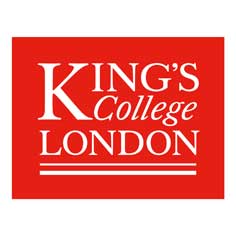
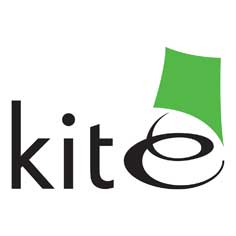
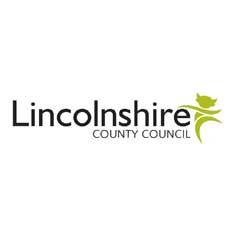
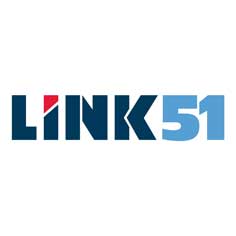
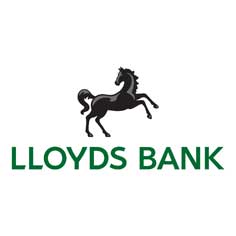

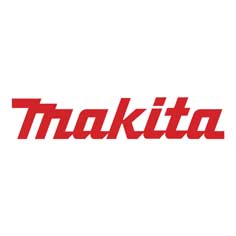
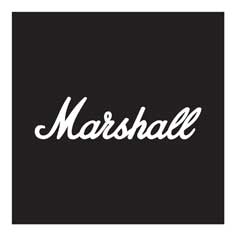
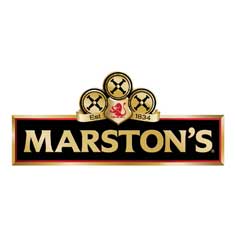
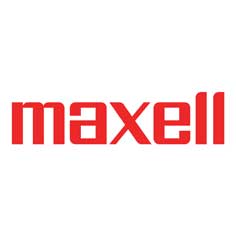
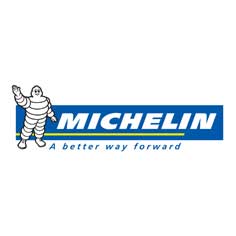
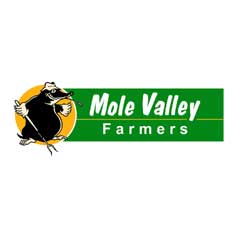
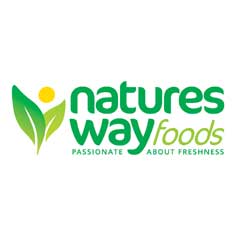
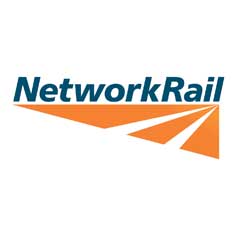
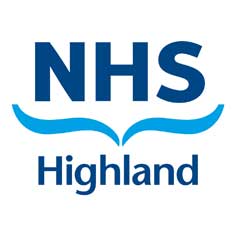
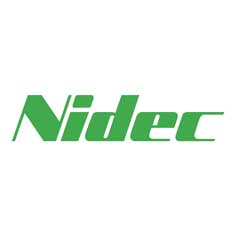
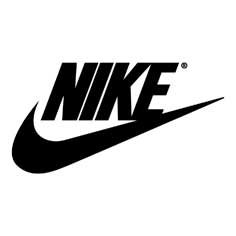
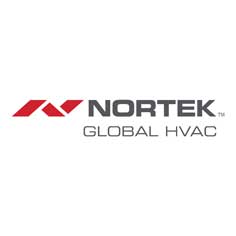
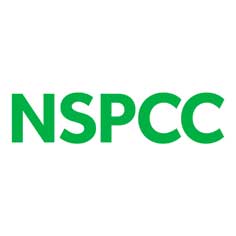
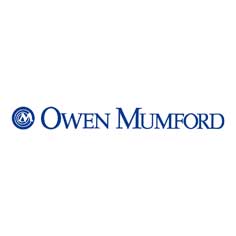
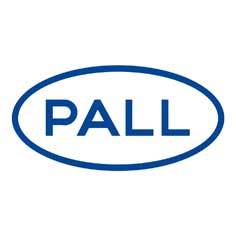
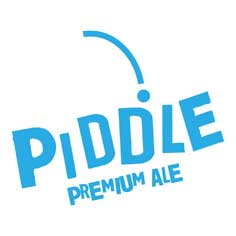
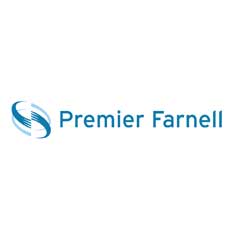
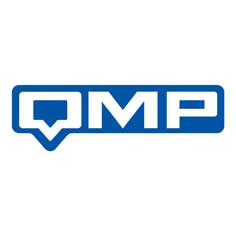
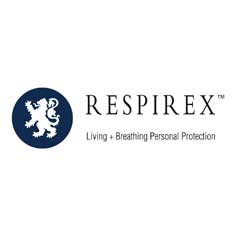
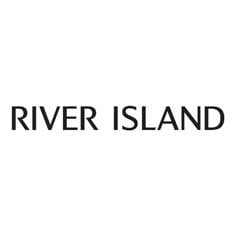

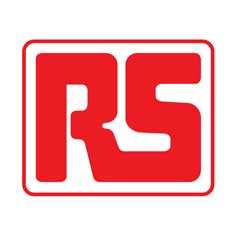
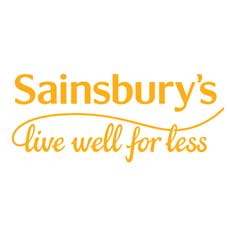
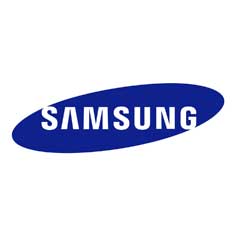
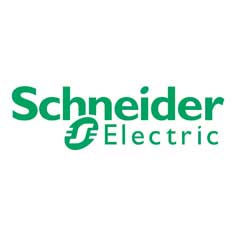
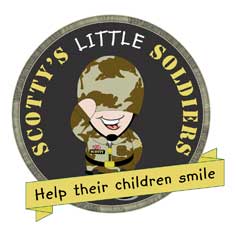
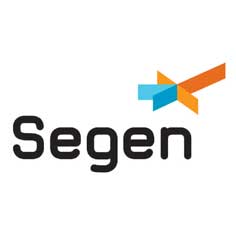
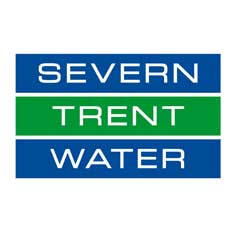
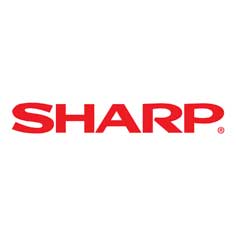
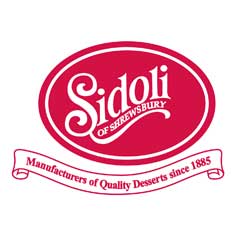
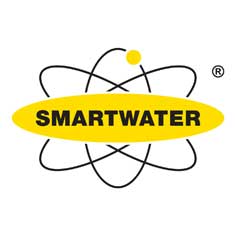
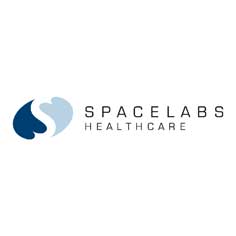
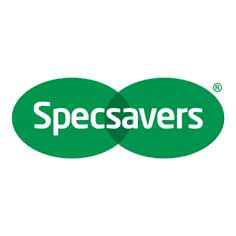
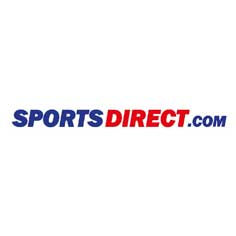
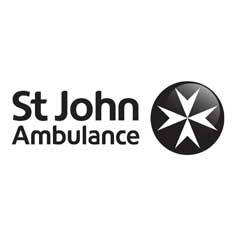
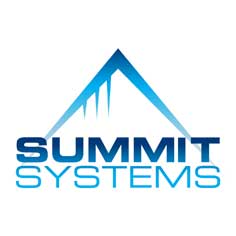

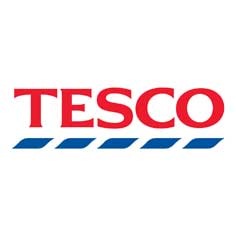
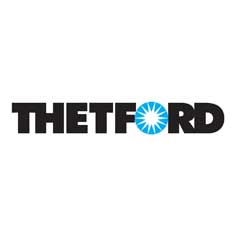
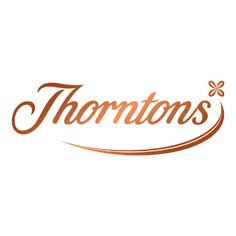
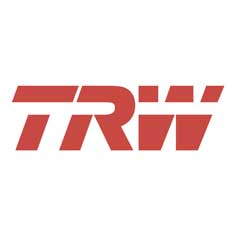
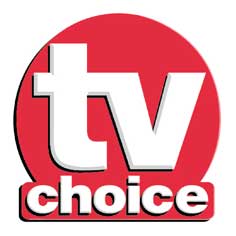
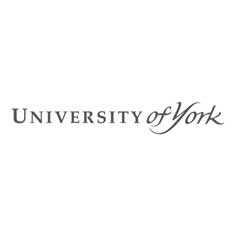
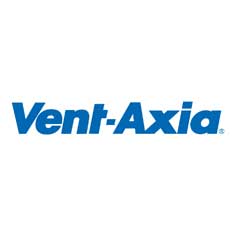
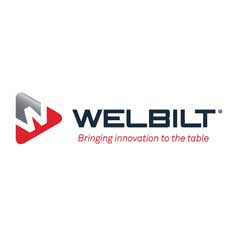
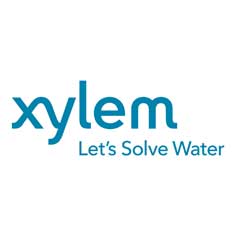

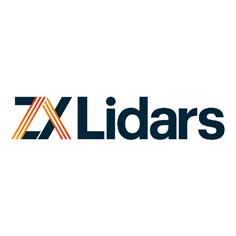
In Mould Decoration
In Mould Decoration offers a branding opportunity providing mouldings, off the press, with full graphics and functionality such as unbroken surfaces with living switches and display windows.
Efficient & Effective Product Marking
Customark as a specialist in product branding is one of the most knowledgeable in the field of In Mould Decoration. Using our print and moulding experience provides unrivalled support for new and existing projects.
The process itself provides tangible process efficiencies and full surface wrap with graphics. The ‘A’ surface of any product can take on the surface property of the films such as Antimicrobial, Hard coat or antiglare. Finished parts off the press without the need for post moulding processing is a significant factor in adopting this technology. The advent of In-Mould structured electronics (IMSE) is the latest development which can incorporate flexible circuits and surface mount components such as LEDs.
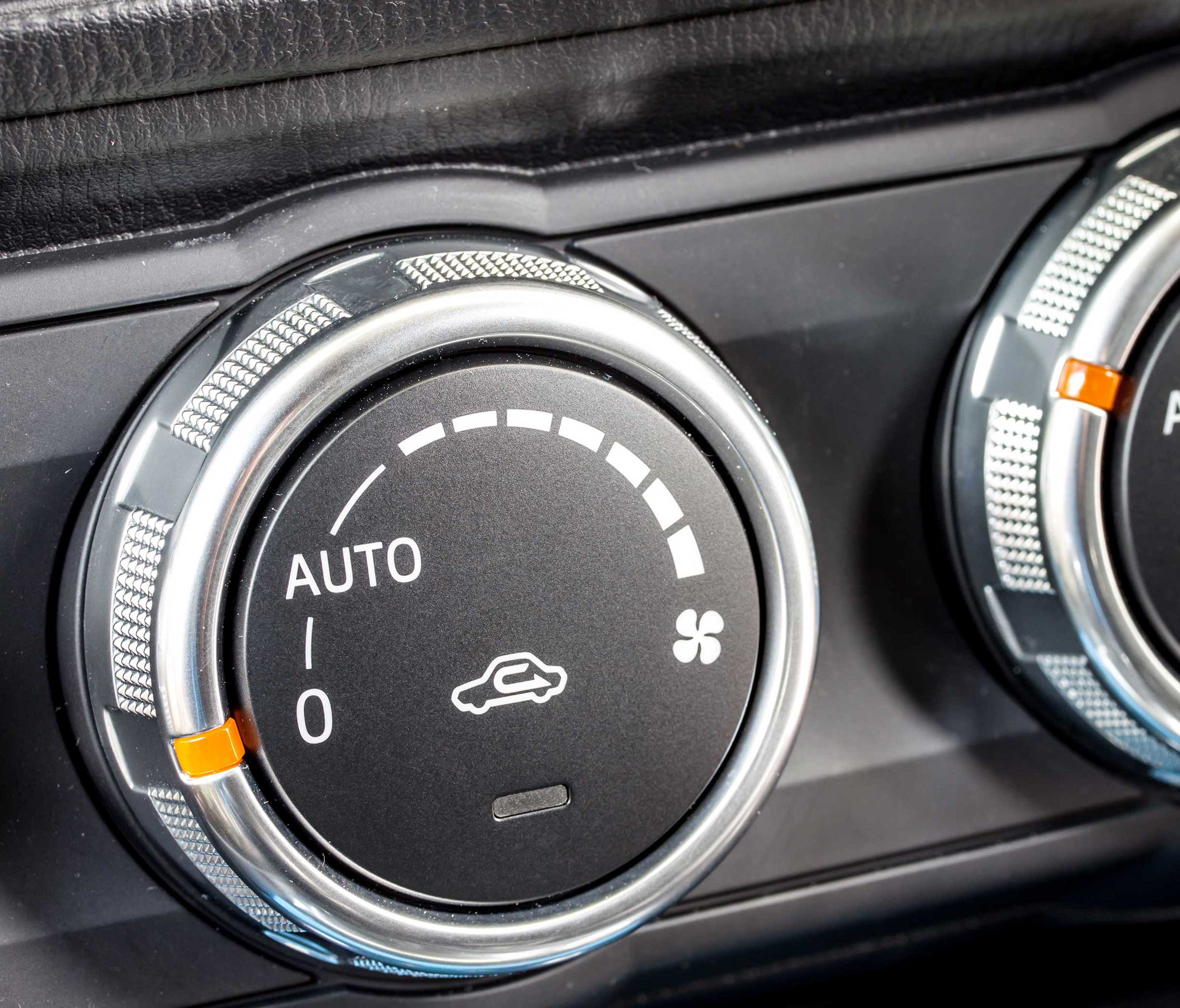
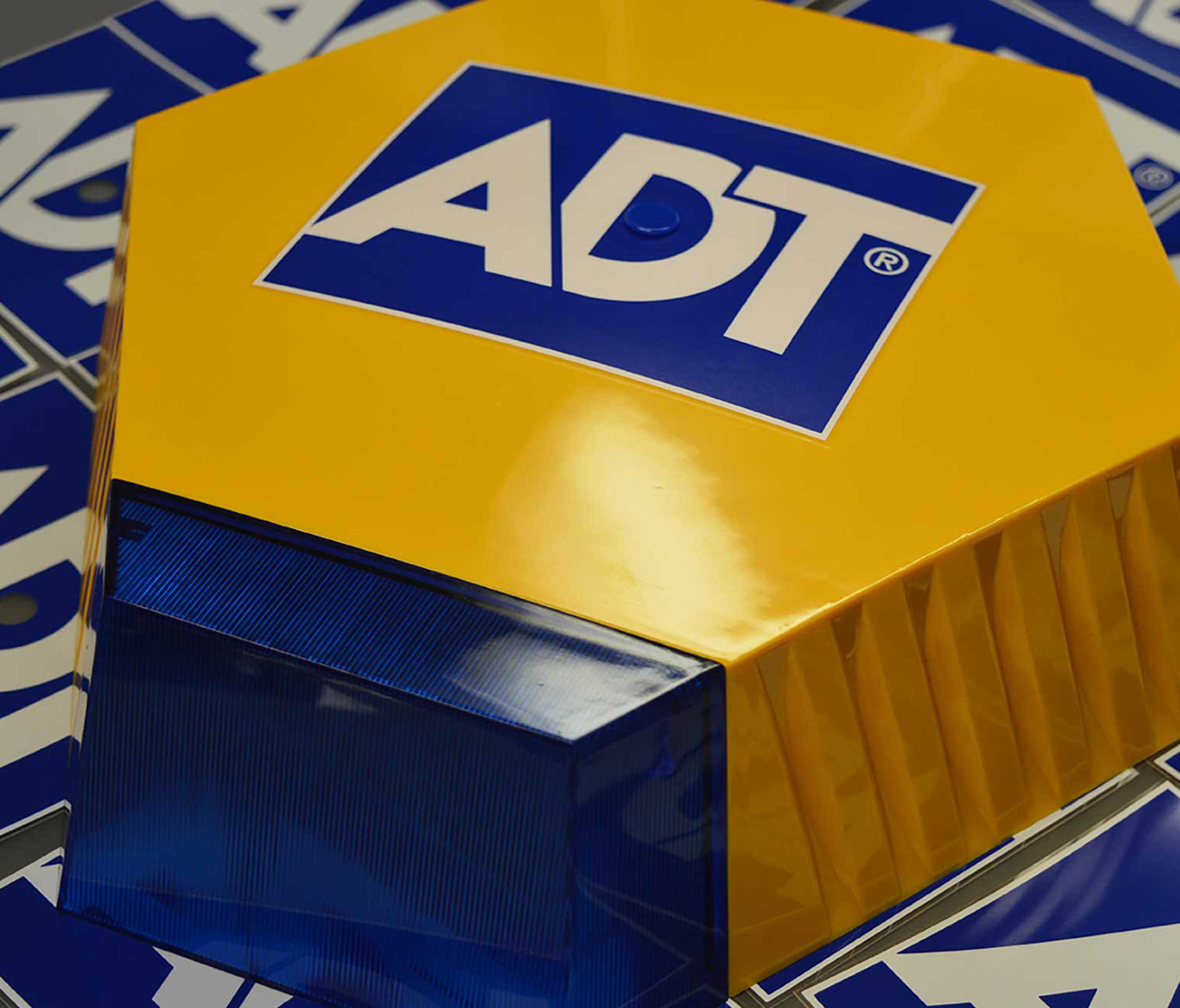
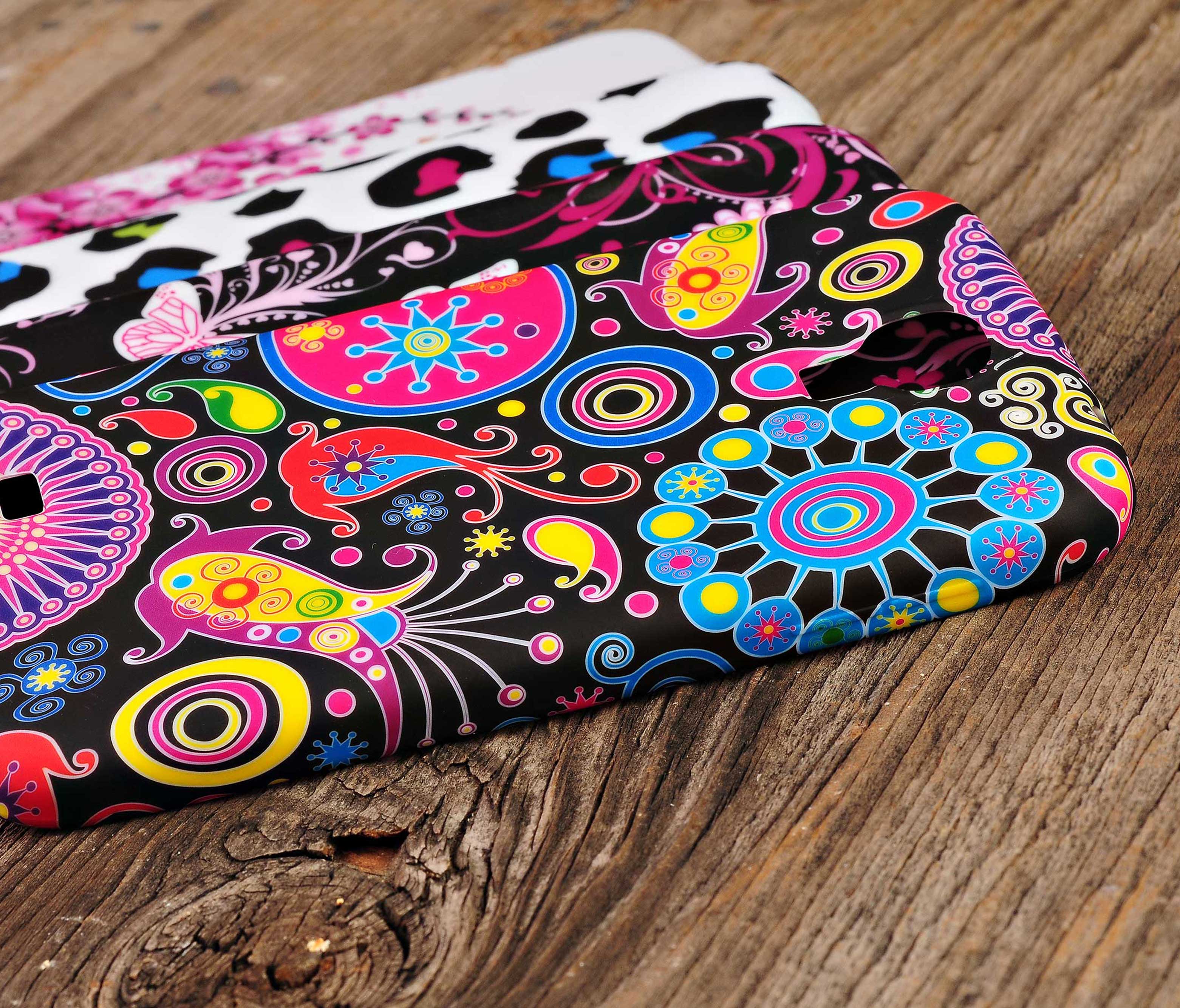
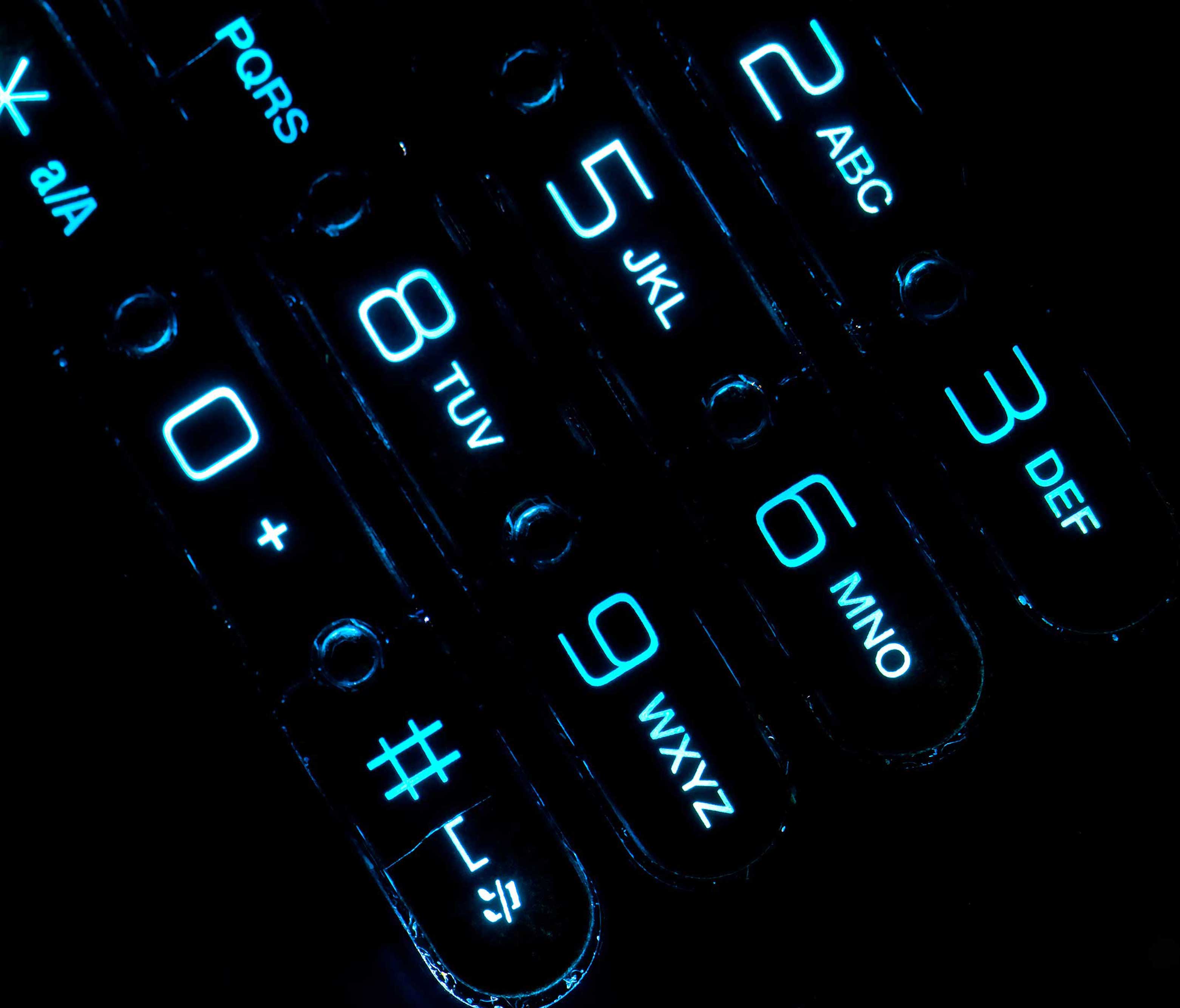
Looking for In Mould Decoration?
Contact our customer support staff today!
In-Mould Decoration (IMD): A Game-Changer in Product Design
In-Mould Decoration (IMD) has been around for years, initially dominating mobile phone lenses and keypads in the late 90s. However, advancements in film, ink, and moulding technology have significantly expanded its potential.
When developing new products, IMD and Film Insert Moulding (FIM) are often briefly discussed but sometimes dismissed due to uncertainty. Success depends on both the expertise of the printer and the understanding of the moulder. Without this knowledge, many companies choose to avoid the process altogether. However, when implemented correctly—combining technical know-how with practical experience—IMD has proven to be an outstanding solution. Once adopted, businesses often integrate it fully into their production process, leveraging its flexibility to enhance both design and manufacturing.
What is IMD?
A simple way to describe IMD is surface-integrated graphics. This technique involves placing a printed film into a mould cavity or using a pre-formed, precisely trimmed applique that seamlessly fits into a mould tool. The result? A sleek, modern design—far superior to outdated manufacturing aesthetics.
IMD offers exceptional functionality, including:
- Clear windows & living switches
- Hard coatings for durability
- Anti-glare & anti-microbial properties
- Hidden-till-lit legends
Unlike traditional methods, IMD delivers a fully finished part straight off the press, eliminating the need for post-printing, dipping, trimming, or coating. The time and cost savings from this alone can be substantial.
Process Qualification – Why It Matters
Early-stage process qualification is key to maximizing IMD’s benefits. The best time to explore IMD is during the initial design phase, before committing to conventional manufacturing methods. Our team has seen firsthand how a comprehensive design review can reveal IMD’s potential, often leading to superior results.
IMD vs. Conventional Manufacturing – Benefits & Challenges
Every production method has its strengths and limitations. To determine the best approach, it’s essential to compare different processes before making a decision. Below, we present a sectional view of a sample front moulding, highlighting the differences between traditional fascia manufacturing and IMD.
One of the biggest concerns with IMD is tooling costs, but in most cases, the investment is quickly recovered through increased efficiency. A single mould tool setup can produce multiple printed appliques in different colours or designs, streamlining production while adding features like self-contained windows and switch buttons. IMD also reduces the need for costly secondary processes, as surface treatments such as anti-scratch, anti-fog, and anti-microbial coatings are integrated directly. In flat film applications, tooling costs are virtually eliminated, making it even more cost-effective.
Despite its advantages, IMD is often misunderstood. Many assume it’s only suitable for high-volume production, but with smart design, low-volume applications can also benefit. Films or appliques can be positioned and later trimmed, offering flexibility without large production runs. Another misconception is that IMD can’t be applied to existing products, yet many mould tools can be modified to accommodate film inserts with minor adjustments to gates and ejection systems. Strategic ink application in high-wear areas further enhances durability.
Material flexibility is another key advantage. Contrary to belief, printed appliques and moulding resins don’t have to match. Advanced inks and lacquers create strong bonds between inserts and moulded parts, allowing for combinations like hard-coated polyester films moulded with ABS. This enables high-performance surface finishes without relying on expensive moulding materials.
As offshore manufacturing costs rise, IMD is becoming a more attractive option for UK-based production. The process is easy to assess, and early discussions come at no cost. If you’re considering IMD for a new or existing product, our team is ready to provide expert advice and help you unlock its full potential.
"*" indicates required fields